
CONSULTING

TESTING

DEVELOPMENT
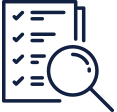
RESEARCH
Vacuum Tribological Tests
Friction, Wear, Coldwelding, Electro-tribology
Tribology in space differs strongly from tribology on earth. Already vacuum itself rules out most solutions used on ground: lubricants evaporate, materials degrade (polymers) or are not corrosion resistant (nitriding steels), most common metallic alloys are subject to strong adhesive wear or cold welding under vibrations, many coatings exhibit much higher friction (e.g. DLC). Hence, selection of material and lubricants in tribological contacts cannot be extrapolated from terrestrial approaches.
The tribological performance for space has to be determined experimentally. AAC runs a wide set of tribological test devices offering time and cost efficient validation starting on material level e.g. vacuum tribometer, cryo-tribometer, high-temperature-vacuum tribometer (up to +700°C), cold welding / fretting test facility. Tests on component level cover ball bearings, journal bearings, gears (e.g Harmonic Drive® gears, planetary gears), magnetic brakes and slip rings. Performance can be validated by properties like friction/torque, wear, electrical contact resistance, gear properties cover e.g. efficiency, stiffness, NLRT and transmission accuracy (all in-sit of TVAC), and finally endurance (life time) and failure analysis are provided.