
BERATUNG

PRÜFUNG

ENTWICKLUNG
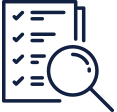
FORSCHUNG
Schadensanalyse und Materialentwicklung
Materialverschlechterung: Rissbildung, Korrosion, Spannungsrisskorrosion, Abnutzung und mehr
Das Team der mikrostrukturellen Charakterisierung verfügt über ein fundiertes Wissen und professionelle Erfahrung auf dem Gebiet der Materialentwicklung und -optimierung, der Schadensanalyse und der Qualitätskontrolle. Wir arbeiten in engem Kontakt mit der ESA, der Luft- und Raumfahrtindustrie und entsprechenden Forschungsinstituten an einer Vielzahl von Metallen und Legierungen wie insbesondere Stählen, Al- und Ti-Legierungen, Verbundwerkstoffen, Beschichtungen und elektronischen Materialien. Ein großer Teil unserer Arbeit ist der Schadensanalyse gewidmet, bei der mechanische, korrosive oder tribologische Phänomene verstanden und mit Produktionsprozessen und Anwendungsumgebungen korreliert werden müssen. Unser motiviertes Team arbeitet ständig an der Erweiterung der Präparations- und Analysemethoden, um auch die schwierigsten Fehler und Schadensfälle lösen zu können.
Die Schadensanalyse dient dazu, die Ursachen für das Versagen von Bauteilen zu ermitteln. Dabei werden verschiedene Analysetechniken eingesetzt, um den Schaden zu untersuchen und die primäre Ursache zu identifizieren, die oft zu weiteren Schäden führt, die lediglich Folgeschäden sind. Erst durch die Identifizierung dieser so genannten Grundursache lassen sich Abhilfemaßnahmen ableiten. Unser Ansatz bei AAC ist es daher, nicht nur das Versagen abzubilden, sondern auch Hinweise für eine mögliche Optimierung von Werkstoffen und Bauteilen zu geben.
Als unabhängiges Labor bieten wir unseren Kunden eine umfassende Fehleranalyse als Dienstleistung an. Die Fehleranalyse kann Folgendes umfassen:
- Analyse von defekten Teilen und Komponenten
- Bewertung von Rissen
- Quantitative Messung der Verschleißraten
- Bewertung der Korrosion
- Interpretation von Ablagerungen auf Funktionsflächen
- Erkennung von Einschlüssen und Defekten, die die mechanischen Eigenschaften beeinflussen können...
Warum eine Fehleranalyse?
Der Zweck einer Fehleranalyse ist die systematische und gründliche Ermittlung der Ursachen von Bauteilausfällen. Ziel ist es, den Schaden an der Wurzel zu verstehen, um geeignete Maßnahmen zur Behebung und zukünftigen Vorbeugung zu ergreifen. Bauteilausfälle führen in der Regel zu wirtschaftlichen Verlusten (Produktionsausfälle, Folgeschäden, Rückrufe usw.) und gefährden möglicherweise die menschliche Gesundheit. Die Klärung von technischen Schäden und deren Ursachen ist eine entscheidende Voraussetzung für die Schadensprävention. Die Schadensanalyse ist daher ein unverzichtbarer Bestandteil des Lernens aus Fehlern.
Bei der Fehleranalyse sind die folgenden Punkte zu berücksichtigen:
- Identifizierung der Grundursache: Die Fehleranalyse hilft dabei, die Ursachen von Schäden zu ermitteln. Dies ermöglicht eine gezielte Behandlung der Hauptursache des Problems.
- Verhütung von Folgefehlern: Die frühzeitige Erkennung und Behebung von Schäden verhindert oft weitere Schäden.
- Ableitung von Abhilfemaßnahmen: Aus den Erkenntnissen einer Fehleranalyse können Maßnahmen abgeleitet werden, um zukünftige Schäden zu verhindern.
- Verbesserung von Prozessen, Materialien und Komponenten: Durch die Analyse von Schäden können Schwachstellen in Prozessen oder Komponenten identifiziert und die Kompatibilität von Materialien bewertet werden. Dies ermöglicht Korrekturmaßnahmen und verbessert die Effizienz und Zuverlässigkeit von Prozessen und Komponenten.
Was kann die Unterstützte Kommunikation bieten?
- Umfassende Fehleranalyse: Unsere systematischen Fehleranalysen beschränken sich nicht nur auf die Untersuchung oberflächlicher Schäden. Wir führen tiefgreifende Untersuchungen durch, um die zugrunde liegenden Ursachen zu ermitteln.
- Expertenwissen: Unser erfahrenes Expertenteam wendet verschiedene Analysemethoden an, um ein breites Spektrum unterschiedlicher Fehlerfälle zu untersuchen.
- Informativer Bericht: Unsere Kunden erhalten einen umfassenden Bericht mit Interpretationen und Schlussfolgerungen, aus denen Aktionspläne abgeleitet werden können.
- Kundenorientierter Ansatz: Jeder Auftrag ist individuell, und deshalb sind unsere Analysen auf die spezifischen Kundenanforderungen zugeschnitten.
Methoden der Fehleranalyse, angeboten von AAC
- Lichtmikroskopie
Mit Hilfe verschiedener moderner Lichtmikroskope (Stereo- und Auflichtmikroskopie) lassen sich Oberflächenstrukturen im Detail darstellen. Dazu gehören unter anderem die Analyse von Bruchflächen, metallographische Untersuchungen, Messung von Schichtdicken in Querschnitten und vieles mehr.
- Oberflächenanalyse:
Oberflächen werden mit optischen Methoden untersucht, um die Rauheit, Welligkeit und Ebenheit einer Oberfläche zu bestimmen. Zum einen können bestimmte Strukturen (z.B. Erhebungen, Täler, Rillen, Poren, Partikelanhaftungen etc.) gemessen werden, zum anderen kann die Oberfläche quantitativ charakterisiert werden (Bestimmung von Ra, Rz und anderen statistischen Oberflächenkenngrößen). Die quantitativen Parameter werden aus 2D-Profilmessungen und 3D-Oberflächenmessungen ermittelt.
Alternativ zu den rein optischen Methoden ist es auch möglich, mit Hilfe komplexer Softwareprogramme aus REM-Bildern ein digitales Oberflächenmodell zu erzeugen und daraus die oben genannten Oberflächenparameter abzuleiten. Dies ermöglicht die Beurteilung von Welligkeit und Rauheit sowie die Vermessung von Strukturen auch auf Oberflächen, die einer optischen Inspektion nicht zugänglich sind (z.B. Vermessung von mikroskopischen Merkmalen auf einer Oberfläche).
- Elektronenmikroskopie:
Mit der Rasterelektronenmikroskopie (REM) werden hochauflösende bildgebende Untersuchungen von Materialproben und Bauteilen durchgeführt. Der Einsatz verschiedener Detektoren liefert unterschiedliche Informationen über die Struktur der untersuchten Oberfläche: Die Topographie lässt sich am besten mit Sekundärelektronen (SE-Detektor) abbilden, während für Materialkontrastbilder rückgestreute Elektronen (BSE-Detektor) verwendet werden. Ein In-Linse-Detektor ermöglicht hochauflösende Bilder mit Auflösungen bis in den nm-Bereich.
Darüber hinaus kann die Probenoberfläche mit einem fokussierten Ionenstrahl (FIB) in-situ im sub-µm-Bereich bearbeitet werden, um den Bereich unmittelbar unter der Oberfläche zu untersuchen. Dies wird z. B. zur Analyse von Schichtstrukturen oder bei der Fehleranalyse eingesetzt. Durch die Abbildung der Probe mit einem Ionenstrahl kann auch die Kornstruktur kontrastreich dargestellt werden.
Die REMs sind auch mit modernen EDX-Systemen ausgestattet, die eine chemische Analyse der untersuchten Oberfläche (oder im FIB-Bereich) ermöglichen. Komplexere Fragestellungen können mit Zeilenscans untersucht werden, die den Konzentrationsverlauf für ausgewählte Elemente zeigen.
Um die kristalline Struktur eines Materials im Detail zu untersuchen, steht die Elektronenrückstreubeugung (EBSD) zur Verfügung. Mit dieser modernen Methode können Mikrostrukturen mit hoher lateraler Auflösung untersucht werden, um folgende Merkmale zu bestimmen: Identifizierung einzelner Phasen, Untersuchung von Korngrenzen, Unterschiede in der Ausrichtung benachbarter Körner, Identifizierung von Ausscheidungen usw.
- Metallographie:
Metallographische Untersuchungen dienen der qualitativen und quantitativen Beschreibung des Gefüges von Werkstoffen mit mikroskopischen Methoden. Für metallographische Analysen werden Querschliffe mit fortschrittlichen Präparationsverfahren (z.B. mechanisch, elektrochemisch, chemisch) hergestellt. An diesen Querschnitten werden dann die Gefüge mittels Lichtmikroskopie oder Rasterelektronenmikroskopie untersucht und Merkmale wie Phasenanteile, Korngrößen, Korngrößenverteilung, Partikelgrößen und Ausscheidungen bestimmt. Dies ermöglicht eine eingehende Analyse der Werkstoffe und erlaubt eine qualitativ hochwertige Versagens- und Bruchanalyse.
- (Mikro-)Härtemessungen:
Die Härte von Metallen, Nichtmetallen und Beschichtungen wird durch Eindringversuche bestimmt: Die Härte ist definiert als der Widerstand gegen das Eindringen eines Prüfkörpers; als Messgröße dient die Größe des bleibenden Abdrucks des Prüfkörpers (Vickers-, Knoop- oder Brinell-Verfahren).
Zur Bestimmung der Einhärtetiefe, der Oberflächenhärtetiefe und der Nitrierhärtetiefe von oberflächengehärteten Stählen wird eine Reihe von Härteeindrücken auf dem polierten Querschnitt vom Probenrand zur Probenmitte hin angebracht. Die entsprechenden Härtetiefen werden aus der so ermittelten Härtetiefenkurve abgeleitet.
Die moderne, dem neuesten Stand der Technik entsprechende Ausrüstung, die bei AAC zur Verfügung steht, ermöglicht die (vollautomatische) Untersuchung der Härte mit Lasten im Bereich von 0,25 g bis 62,5 kg. Darüber hinaus können Harness-Mappings (z. B. Linien-Scans, Matrix-Scans) durchgeführt werden, um die laterale Verteilung der mechanischen Eigenschaften zu bewerten.